Share this Post
What is the supply chain?
To appreciate how using supply chain analytics will lead to better business decisions, take a look first at the supply chain itself.
Most people involved in the supply chain will recognize there is seven step process that needs to be followed.
1. Procurement
2. Inbound logistics
3. Parts inventory
4. Manufacturing
5. Finished goods inventory
6. Fulfillment (customer’s order to delivery)
7. Outbound logistics
This handy illustration shows the relationship between each link in the chain.
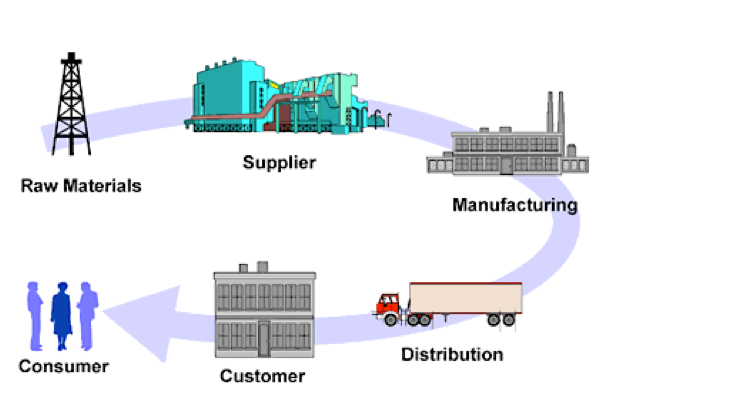
Source: Data Science Central
The process starts with the raw materials. Where are they coming from? How much do they cost and how does the price vary? Can price changes be predicted? What are the logistics involved for those raw materials to get to the supplier and to then reach the manufacturing plant.
There needs to be a tight control on the parts inventory so the manufacturing process can meet changes in demand. Manufacturing can be severely impacted by adversity at any point along the path from raw materials to parts inventory. Not having essential parts can bring manufacturing to a standstill. Downtime. Money hemorrhaging from the business. Unhappy customers being kept waiting. Factory staff twiddling their thumbs and scratching their heads.
Likewise, the output needs to be controlled so the finished goods inventory is efficiently matched to what is needed. A backlog of goods in the factory with nowhere to go is no good for anyone.
Finally, assuming that everything is running smoothly up to and including manufacturing the goods, those goods need a reliable and fluid route to the customers and ultimately reaching the consumers.
What are supply chain analytics?
The more information that can be obtained about every point in the chain, the easier it is to find efficiencies and make the operation run smoother. That means lots of data gathering. From the demand side it means understanding the peaks and troughs, and understanding consumer behavior.
Further up the chain, it means understanding other eventualities that could affect supply to customers. The logistics of shipping goods from the factory can be affected by multiple factors. The cost of oil and fuel can vary, and of course this won’t just affect the direct cost of shipping goods from the factory. It will also eventually affect the cost of the raw materials being shipped to the factory and the cost of manufacturing.
Where are the goods being manufactured and where are they being shipped to? This is a big question because there are implications on the transport costs because of fuel and the geography also needs to be kept in mind.
Put simply, supply chain analytics involves lots and lots of measurement of as much as can be measured at the different points of the supply chain. This data can be analysed to detect trends and to spot where savings can be made, where the whole process can be optimized to run more efficiently.
What are the business benefits?
Supply Chain Analysis is a tool for making the supply chain more efficient by using an agile methodology. Measure, record, learn, change, implement and measure for improvement. Repeat. It is easy to see that the data will become more meaningful, the more there is. Throw a dice six times and it may show a sequence such as three, three, one, six, four, three. The fact that any one number has a six to one chance of being seen – while a known probability – doesn’t actually reveal itself in action perfectly until the dice is thrown (in theory) an infinite number of times, but the trend will certainly be more clearly observable after a few dozen throws.
In this way, the process of supply chain analysis is said to mature as more data from the different points is gathered and the flow becomes increasingly streamlined.
What are the facts?
The fact is that a diverse range of businesses have become more profitable thanks to the use of supply chain analytics. From Walmart to Dell Computer the technique has led to marked success. Supply chain analytics can easily be credited with enabling Amazon to take the world by storm and change the retail landscape as they have.
Unilever has managed to double the size of its business and reduce its environmental impact, and its management team lay the credit firmly at the door of its supply chain improvements. By establishing a virtual manufacturing network, Unilever was able to quickly support fluctuations in local demand and tap into global capacity as needed through flexible manufacturing.
Predicting the future
Supply chain analytics is not just about recognizing what has been happening and learning from the past. For any organization to truly reap the benefits there has to be an element of understanding what could happen and even what will happen.
Vulnerabilities need to be identified and addressed while opportunities need to be looked out for and capitalized on.
The supply chain can be incredibly complex especially with larger global organizations and the management at the top don’t always have total visibility of all the processes in the chain. That can be fatal. The consequences of a lack of transparency and a deep and complex supply chain could mean, as recently publicized, that the squeaky clean supplier that a global retailer is using may, itself, be relying on less savory suppliers that are involved in child labor for example.
Back in 2011 when Japan suffered a major earthquake, many Japanese factories had to shut down because they were relying on parts that were not arriving because their suppliers had been affected by the disaster.
The future is rosy
For organizations using supply chain analytics the future is bright. Firstly, their supply chains will become more agile and robust. As more data becomes available, more insights will be gained by companies on how to improve.The kind of insights gained will be rich and varied such as how reliable a particular supplier is.
The benefits of supply chain analysis are many but as the thinking behind it evolves so will the information that can be gleaned, and that mean even more benefits for industry.
Share this Post